ISO 9001:2015 Quality Management System Certification
I. INTRODUCTION TO ISO 9001
ISO 9001:2015 is an international standard that specifies requirements for a Quality Management System (QMS). This standard is designed to ensure the capability to provide products and services that meet customer and stakeholder requirements, while also facilitating the flow of goods in both domestic and international trade. Since its first issuance in 1987, ISO 9001 has become the most widely adopted standard, with 1,471,685 certifications worldwide (ISO Survey of Certifications - 2023).
Amid intensifying competition, ISO 9001:2015 not only helps businesses ensure the quality of products and services—a critical factor for survival—but also serves as a key to achieving breakthroughs and asserting their market position. Adopting this international standard offers a comprehensive solution, enabling organizations to enhance management effectiveness and improve quality, thereby building strong trust among customers and partners.
ISO 9001:2015 is the core standard of the ISO 9000 family, defining requirements for establishing, implementing, and certifying a quality management system. Other supportive standards in the ISO 9000 family include: ISO 9000:2015 Fundamentals and Vocabulary, which standardizes terminology and concepts in quality management; ISO 9004:2018 Guidelines for achieving sustainable success, providing insights into effective quality management approaches; and ISO 19011:2018 Guidelines for auditing management systems, which outlines the principles, processes, and methods required to conduct internal audits.
Apart from ISO 9001:2015, there are also other quality management system standards specifically designed for certain industries, including:
- ISO 13485:2016 Quality management systems for medical devices.
- ISO 29001:2020 Quality management systems for petroleum, petrochemical and natural gas industries.
- IATF 16949:2016 Automotive Quality Management System Standard.
- AS9100D Quality management systems for aviation, space, and defense Organizations.
Since its initial release in 1987, ISO 9001 has undergone several revisions to align with advances in technology and the global market's evolving demands:
ISO 9001:2015 is an international standard that specifies requirements for a Quality Management System (QMS). This standard is designed to ensure the capability to provide products and services that meet customer and stakeholder requirements, while also facilitating the flow of goods in both domestic and international trade. Since its first issuance in 1987, ISO 9001 has become the most widely adopted standard, with 1,471,685 certifications worldwide (ISO Survey of Certifications - 2023).
Amid intensifying competition, ISO 9001:2015 not only helps businesses ensure the quality of products and services—a critical factor for survival—but also serves as a key to achieving breakthroughs and asserting their market position. Adopting this international standard offers a comprehensive solution, enabling organizations to enhance management effectiveness and improve quality, thereby building strong trust among customers and partners.
ISO 9001:2015 is the core standard of the ISO 9000 family, defining requirements for establishing, implementing, and certifying a quality management system. Other supportive standards in the ISO 9000 family include: ISO 9000:2015 Fundamentals and Vocabulary, which standardizes terminology and concepts in quality management; ISO 9004:2018 Guidelines for achieving sustainable success, providing insights into effective quality management approaches; and ISO 19011:2018 Guidelines for auditing management systems, which outlines the principles, processes, and methods required to conduct internal audits.
Apart from ISO 9001:2015, there are also other quality management system standards specifically designed for certain industries, including:
- ISO 13485:2016 Quality management systems for medical devices.
- ISO 29001:2020 Quality management systems for petroleum, petrochemical and natural gas industries.
- IATF 16949:2016 Automotive Quality Management System Standard.
- AS9100D Quality management systems for aviation, space, and defense Organizations.
Since its initial release in 1987, ISO 9001 has undergone several revisions to align with advances in technology and the global market's evolving demands:
- ISO 9001:1987 - The first version, focusing on production process control, primarily based on U.S. military standards (MIL-Q-9858A), NATO's AQAP-1, and the British industrial standard BS 5750.
- ISO 9001:1994 - An update with a stronger focus on process control and quality improvement but still oriented toward implementing documented procedures.
- ISO 9001:2000 - A significant shift from process control to quality management, emphasizing process management, customer satisfaction, and continuous improvement.
- ISO 9001:2008 - This version mainly refined existing requirements for clarity and ease of use, with no substantial changes to content.
- ISO 9001:2015 - The current version features a new structure for easier integration with other management systems like ISO 14001 and ISO 45001. It also emphasizes risk-based thinking, leadership, and more effective improvement to meet growing business demands.
- ISO 9001:2026 - The revised version is currently under development with numerous enhancements to align with the evolving context and current market demands. The ISO 9001:2026 standard is expected to be officially released in September 2026.
ISO 9001:2015 requirements include:
- Context of the organization: Understanding and managing internal and external factors that can influence quality objectives, including stakeholder requirements.
- Leadership: Leadership plays a crucial role in commitment, direction-setting, and promoting a quality culture within the organization, ensuring that the quality management system is integrated into organizational processes.
- Planning: Identify and address risks and opportunities, set clear quality objectives, and plan changes as necessary to meet these objectives.
- Support: Ensure adequate resources, including personnel, infrastructure, and work environment. Documentation systems, knowledge management, and communication must support processes.
- Operation: Manage and control production and service delivery processes to meet customer requirements, including quality control, reviewing, and confirming product requirements, as well as monitoring and inspecting products.
- Performance Evaluation: Monitoring, measuring, analyzing, and evaluating the effectiveness and suitability of the quality management system, including conducting internal audits and management reviews.
- Improvement: Regular actions to improve the quality management system, including handling nonconformities and taking corrective actions to prevent recurrence.
.png)
Representation of the structure of this International Standard in the PDCA cycle
The Process of establishing and implementing an ISO 9001:2015 Quality Management System in organizations and enterprises generally includes the following basic steps:
- Assessment of Current Status and Leadership Commitment: Conduct an assessment of the organization’s current structure and management to identify the processes and documentation that need to be supplemented according to the requirements of ISO 9001:2015. Leadership must commit to providing the necessary resources and set a clear direction for implementing the quality management system.
- Planning and Training: Develop a plan that includes tasks, timelines, and resources to implement the quality management system according to ISO 9001:2015. Organize training for employees to help them understand the requirements of ISO 9001:2015, how to apply these to daily work, and conduct internal system evaluations.
- Reviewing, Supplementing, Standardizing Processes, and Developing Documentation: Review, supplement, and standardize management, operational, and support processes according to ISO 9001:2015 requirements. Develop a documentation system to ensure consistency in task execution and facilitate transparent, convenient internal evaluations.
- Implementing the Quality Management System: The processes and documents within the quality management system should be integrated into the organization's daily operations. Employees must adhere to and execute processes accurately to ensure the system’s effectiveness and efficiency. Establish monitoring and supervision mechanisms to promptly detect and correct errors, ensuring the quality management system operates effectively.
- Internal audit and corrective actions: Train an internal audit team and conduct evaluations to identify areas for improvement in the system and ensure that all processes comply with ISO 9001:2015 requirements. Implement prompt and effective corrective actions for issues identified through internal audits, monitoring, and customer feedback to continually enhance and perfect the system.
- Certification Evaluation, Maintenance, and Continuous Improvement: Select a reputable certification body that meets the organization’s needs to conduct evaluations and issue the ISO 9001:2015 certificate. Certification evaluations are conducted according to the procedures of the certification body. Certification is granted when the system fully meets the certification requirements. Continuously apply the system’s processes, monitor them, and regularly make improvements to enhance the system's effectiveness, aligning with the ISO 9001:2015 objectives.
ISO 9001:2015 is considered an effective tool for improving management efficiency, ensuring product quality, and enhancing competitiveness for businesses. However, during implementation, many organizations face challenges and fail to achieve the expected benefits. Below are some common difficulties encountered by organizations and businesses:
(i) Insufficient Commitment and Engagement from Leadership
(i) Insufficient Commitment and Engagement from Leadership
- Misconceptions about the role of the quality management system: Some leaders do not fully understand the importance of the system, viewing the implementation of ISO 9001 as merely a formal procedure to obtain certification. This results in a lack of direction and determination in building and operating the system.
- Limited involvement in establishing and monitoring: Leaders are often minimally involved in establishing processes and procedures or in monitoring the implementation of quality management system requirements. This leads to a failure to identify emerging issues and understand the actual impact of the system, hindering timely decision-making and improvement efforts.
- Lack of resource allocation: The implementation and maintenance of a quality management system are significantly impacted if adequate resources (human, financial, and time) are not proportionally allocated.
(ii) Challenges in Understanding Standard Requirements
- Generalized language: ISO 9001 is designed to be applicable to all types of organizations and businesses, resulting in generalized language that can be difficult to interpret and apply in specific situations.
- Lack of examples and specific guidance: The standard provides principles and requirements but lacks illustrative examples or detailed instructions, leaving many businesses, especially small and medium-sized enterprises (SMEs), struggling to implement them.
- Translation challenges: Translating the standard from English to Vietnamese can reduce clarity, making it difficult for newcomers to understand and visualize the actions required.
(iii) Development of Quality Management System Processes and Procedures that Are Cumbersome and Inefficient
- Lack of document drafting skills: In many cases, managers lack experience and writing skills to transform current tasks into clear and applicable processes.
- Mechanical application of sample procedures: Many businesses adopt template procedures from consulting firms without testing or adjusting them to fit their specific context. This often results in procedures that do not meet job requirements, hindering the implementation process.
- Improper assignment of process development: The development of procedures is often assigned to individuals who lack a deep understanding of the tasks or processes involved. As a result, the established procedures lack necessary control requirements, making monitoring and implementation challenging. In some cases, non-compliance goes unnoticed or unaddressed.
- Insufficient consideration in creating rules and templates: Rules and templates sometimes include unnecessary content, leading to frustration and dissatisfaction among those tasked with implementation.
Quality management systems include mechanisms to help businesses evaluate effectiveness, efficiency, and implement timely improvements, such as internal audits, monitoring of errors and customer satisfaction, and management reviews. However, in practice, these activities are often conducted superficially and fail to deliver the expected results:
- Ineffective periodic internal audits: In many organizations, internal audits are ineffective due to auditors lacking the skills and understanding of the processes being audited. Consequently, audit findings fail to identify errors or shortcomings that need improvement, even though these issues are often unavoidable in practice.
- Lack of monitoring and evaluation of system performance indicators: A well-designed and effectively operated quality management system helps reduce errors and increase customer satisfaction, both internally and externally. However, many businesses fail to monitor or evaluate these indicators, making it difficult to assess the system's actual effectiveness and implement timely corrective actions.
- Ineffective management reviews: Management reviews play a critical role in evaluating the effectiveness and efficiency of the system after each implementation cycle (typically once a year). However, many leaders fail to fully understand the significance of this activity and are not provided with sufficient information and data to make appropriate corrective and improvement decisions.
II. CERTIFICATION PROCESS
1. Certification registration: To obtain ISO 9001:2015 certification, organizations need to contact GIC Vietnam for registration guidance. Organizations then complete the application and submit it to GIC Vietnam with the required certification documents.
2. Audit program and auditor assignment: GIC Vietnam develops an assessment program, clearly defining the activities needed to confirm that the organization’s quality management system (QMS) meets certification requirements. Auditors are selected based on expertise relevant to the assessment field, with additional technical auditors added as necessary.
3. Assessment process: Conducted in two stages:
Stage 1: Review documentation, conditions, scope, and the organization's readiness for stage 2 assessment.
Stage 2: Evaluate the implementation and effectiveness of the management system, including the following steps: Opening Meeting → Department/Unit Evaluation → Assessment Report Preparation → Closing Meeting.
4. Assessment report and corrective actions: The organization must implement corrective actions for errors and deficiencies found during the assessment, ensuring all requirements are fully met.
5. Review and certification issuance: The Certification Council reviews the assessment records to decide on certification approval or denial. ISO 9001:2015 certification is issued once the organization fully meets the requirements and is valid for three years, with periodic monitoring required to maintain validity.
III. BENEFITS OF CHOOSING GIC CERTIFICATION
- International recognition: GIC is a reputable certification body widely recognized around the world, holding accreditation from leading organizations such as UKAS (United Kingdom), CPSC (United States), JAS-ANZ (Australia–New Zealand), SAAS (SAI), VICAS (Vietnam), SAC (Singapore), CNAS (China), and many others. Certificates issued by GIC are not only valid in Vietnam but also recognized internationally through accreditation marks and mutual recognition arrangements (MRA) under the International Accreditation Forum (IAF) and the Asia Pacific Accreditation Cooperation (APAC). This enables businesses to easily access global markets and enhance their brand reputation.
- High-quality services at competitive costs: GIC Vietnam provides certification services according to the strict standards of Europe and North America, ensuring that enterprises’ products and services meet international benchmarks. Not only does GIC deliver superior service quality, but it also offers reasonable, competitive fees, allowing businesses to optimize resources while still achieving global recognition.
For ISO 9001 certification inquiries, please contact:
GIC VIETNAM
12F, 14 Lang Ha Building, Ba Dinh District, Hanoi
Tel: 024.6275 2268, Fax: 024.6275 2269, Email: tuandm@gicvn.vn
Ho Chi Minh City Office: R502, 160 Nam Ky Khoi Nghia, Tel: 028.39307936
.png)
2. Audit program and auditor assignment: GIC Vietnam develops an assessment program, clearly defining the activities needed to confirm that the organization’s quality management system (QMS) meets certification requirements. Auditors are selected based on expertise relevant to the assessment field, with additional technical auditors added as necessary.
3. Assessment process: Conducted in two stages:
Stage 1: Review documentation, conditions, scope, and the organization's readiness for stage 2 assessment.
Stage 2: Evaluate the implementation and effectiveness of the management system, including the following steps: Opening Meeting → Department/Unit Evaluation → Assessment Report Preparation → Closing Meeting.
4. Assessment report and corrective actions: The organization must implement corrective actions for errors and deficiencies found during the assessment, ensuring all requirements are fully met.
5. Review and certification issuance: The Certification Council reviews the assessment records to decide on certification approval or denial. ISO 9001:2015 certification is issued once the organization fully meets the requirements and is valid for three years, with periodic monitoring required to maintain validity.
III. BENEFITS OF CHOOSING GIC CERTIFICATION
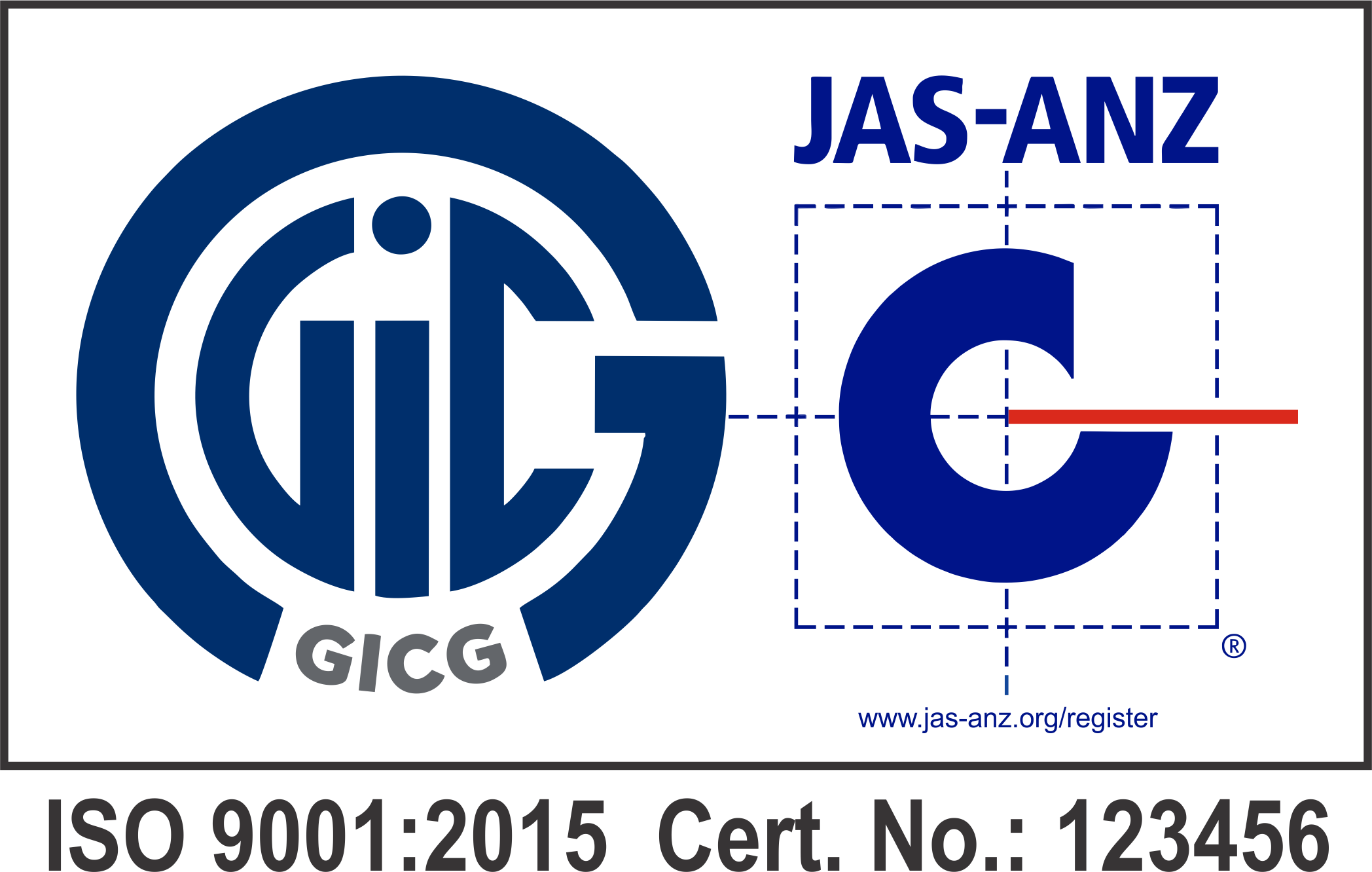
- High-quality services at competitive costs: GIC Vietnam provides certification services according to the strict standards of Europe and North America, ensuring that enterprises’ products and services meet international benchmarks. Not only does GIC deliver superior service quality, but it also offers reasonable, competitive fees, allowing businesses to optimize resources while still achieving global recognition.
For ISO 9001 certification inquiries, please contact:
GIC VIETNAM
12F, 14 Lang Ha Building, Ba Dinh District, Hanoi
Tel: 024.6275 2268, Fax: 024.6275 2269, Email: tuandm@gicvn.vn
Ho Chi Minh City Office: R502, 160 Nam Ky Khoi Nghia, Tel: 028.39307936